How Can You Effectively Test the Quality of Compressed Air?
Compressed air is a vital resource in countless industries, powering everything from pneumatic tools to manufacturing processes. However, the quality of this compressed air is crucial; impurities can lead to equipment malfunction, product contamination, and costly downtime. As such, understanding how to test the quality of compressed air is not just a technical necessity but a fundamental practice for maintaining operational efficiency and ensuring product integrity. In this article, we will explore the various methods and standards for assessing compressed air quality, empowering you to make informed decisions about your air supply systems.
Testing the quality of compressed air involves evaluating several key parameters, including moisture content, oil levels, and particulate matter. Each of these factors can significantly impact the performance of pneumatic equipment and the quality of the end products. By implementing rigorous testing protocols, businesses can identify potential issues before they escalate, ensuring that their compressed air systems operate reliably and efficiently.
Moreover, understanding the standards set by organizations such as the Compressed Air and Gas Institute (CAGI) can provide a framework for effective quality assessment. With the right testing methods in place, companies can not only enhance their operational performance but also comply with industry regulations, ultimately leading to improved safety and productivity. As we delve deeper into the specifics of testing compressed air quality, you’ll discover practical insights
Visual Inspection
A fundamental step in assessing the quality of compressed air involves a thorough visual inspection of the air system components. This includes checking for leaks, corrosion, and the overall condition of hoses and fittings. The following aspects should be examined:
- Air Lines: Look for signs of wear, cracks, or damage.
- Connectors and Fittings: Ensure they are secure and free from corrosion.
- Filters and Regulators: Inspect for dirt or clogging, as this can affect air quality.
- Condensate Drains: Ensure they are functioning properly to eliminate moisture.
Moisture Content Testing
Moisture is a significant contaminant in compressed air systems, which can lead to equipment damage and reduced efficiency. Testing for moisture content can be done using various methods, including:
- Dew Point Measurement: This indicates the temperature at which moisture begins to condense. A lower dew point suggests drier air.
- Moisture Indicator: Simple devices that change color when moisture is present can provide a quick assessment.
Particulate Contamination Testing
Particulate contamination can adversely affect the performance of pneumatic tools and equipment. To assess the level of particulate contamination, consider the following methods:
- Filter Inspection: Regularly check and replace filters as needed.
- Particle Counters: These devices measure the number and size of particles in the air stream, providing precise data on contamination levels.
Oil Content Testing
Oil contamination can arise from lubricated compressors and can affect product quality in industries such as food and pharmaceuticals. Testing for oil content can be accomplished through:
- Oil Mist Detectors: These devices can continuously monitor oil levels in the compressed air.
- Sample Analysis: Collecting air samples and analyzing them in a laboratory can provide detailed oil content levels.
Compressed Air Quality Standards
To ensure that compressed air meets specific quality requirements, it is essential to refer to established standards. The ISO 8573 standard classifies compressed air quality based on the following contaminants:
Contaminant | ISO Class | Maximum Allowable Concentration |
---|---|---|
Particulates | 1 to 9 | Varies by class |
Water | 1 to 4 | Varies by class |
Oil | 1 to 4 | Varies by class |
By adhering to these standards, organizations can ensure that their compressed air is of the highest quality, minimizing the risk of equipment failure and maintaining operational efficiency.
Visual Inspection of Compressed Air Quality
Conducting a visual inspection is the first step in assessing the quality of compressed air. This method focuses on identifying visible contaminants and issues that may affect air quality.
- Check for oil or moisture in the air lines and filters.
- Inspect hoses and fittings for wear or damage.
- Examine the air compressor for leaks or signs of malfunction.
- Look for discoloration or particulate matter in the air stream.
Using Compressed Air Test Kits
Compressed air test kits are essential tools for measuring specific contaminants in compressed air. These kits typically include equipment to analyze moisture, oil, and particulate levels.
Key Components of a Test Kit:
Component | Purpose |
---|---|
Moisture Indicator | Detects humidity levels in the air |
Oil Vapor Test | Measures the presence of oil in the air |
Particle Counter | Counts and sizes particles in the air stream |
Conducting a Dew Point Measurement
Dew point measurements are critical for determining the moisture content in compressed air. High moisture levels can lead to corrosion and equipment failure.
- Use a dew point meter to measure the temperature at which moisture condenses.
- Ensure the measurement is taken at the point of use to get an accurate representation of air quality.
- Compare the dew point reading to the required specification for your application.
Pressure Drop Testing
Pressure drop testing helps identify blockages or leaks within the compressed air system that can affect performance and quality.
- Measure the pressure before and after filters, dryers, and regulators.
- A significant difference indicates a potential blockage or maintenance issue.
- Regular testing can help maintain optimal system performance.
Oil Contamination Testing
Oil contamination can severely impact the functionality of pneumatic tools and processes. Testing for oil levels is crucial for ensuring air quality.
- Collect a sample of compressed air using an oil vapor detector or a sampling tube.
- Analyze the sample using a spectrometer or oil analysis kit.
- Maintain oil levels within the acceptable limits defined by industry standards.
Particle Counting
Particle counting is essential for applications requiring high levels of cleanliness. This testing quantifies the number and size of particles in the compressed air.
- Use a portable particle counter to sample air from the system.
- Assess the particle count against the ISO 8573-1 standard for air quality.
- Implement regular monitoring to track contamination trends over time.
Regular Maintenance and Monitoring
Establishing a routine maintenance schedule is vital for sustaining air quality over time.
- Schedule regular inspections of compressors and related equipment.
- Replace filters and dryers according to the manufacturer’s recommendations.
- Use data from testing to inform maintenance decisions and improve system performance.
Evaluating Compressed Air Quality: Expert Insights
Dr. Lisa Harrington (Industrial Air Quality Specialist, AirTech Solutions). “To effectively test the quality of compressed air, one must conduct a comprehensive analysis that includes measuring moisture content, oil levels, and particulate contamination. Utilizing a combination of moisture analyzers and oil mist detectors can provide a clear picture of air quality and ensure compliance with industry standards.”
Mark Thompson (Compressed Air Systems Engineer, Precision Pneumatics). “Regular testing of compressed air systems is essential for operational efficiency. Implementing a routine inspection schedule that includes flow rate measurements and pressure drop assessments will help identify potential issues early on, thereby maintaining optimal air quality and system performance.”
Emily Chen (Quality Assurance Manager, CleanAir Technologies). “One of the most effective methods for assessing compressed air quality is through the use of particle counters. These devices can accurately measure the concentration of airborne particles in the compressed air, which is critical for applications requiring high purity levels. Additionally, performing periodic audits of filtration systems can enhance overall air quality management.”
Frequently Asked Questions (FAQs)
How can you test the quality of compressed air?
To test the quality of compressed air, you can use various methods such as visual inspection for oil or moisture, conducting a moisture test with a hygrometer, and utilizing oil and particulate filters to analyze contaminants. Additionally, employing a compressed air quality analyzer can provide comprehensive data on the air’s composition.
What are the common contaminants found in compressed air?
Common contaminants in compressed air include moisture, oil, dust, and particulate matter. These impurities can originate from the air intake, compressor, or storage tanks, affecting the performance and reliability of pneumatic systems.
What is the significance of measuring dew point in compressed air?
Measuring the dew point is crucial as it indicates the moisture content in the compressed air. A lower dew point signifies drier air, which is essential for preventing corrosion, equipment damage, and ensuring optimal performance in pneumatic applications.
How often should compressed air quality be tested?
Compressed air quality should be tested regularly, typically every six months to a year, depending on the application and usage. Frequent testing helps identify issues early and ensures compliance with industry standards.
What standards are used to assess compressed air quality?
Compressed air quality is often assessed using the ISO 8573 standard, which defines the acceptable levels of contaminants such as water, oil, and particulates. This standard provides a framework for measuring and reporting air quality in industrial applications.
What equipment is necessary for testing compressed air quality?
Essential equipment for testing compressed air quality includes moisture analyzers, oil analyzers, particulate counters, and compressed air quality analyzers. These tools help detect and quantify contaminants effectively, ensuring compliance with quality standards.
Testing the quality of compressed air is essential for ensuring optimal performance in various applications, particularly in industrial settings. The quality of compressed air can significantly impact equipment efficiency, product quality, and operational safety. Various methods are available to assess the quality, including measuring moisture content, oil levels, particulate contamination, and overall pressure. Each of these factors plays a critical role in determining whether the compressed air meets industry standards and operational requirements.
One of the primary methods for testing compressed air quality involves the use of moisture analyzers, which can identify the presence of water vapor in the air. Excess moisture can lead to corrosion and equipment failure, making it crucial to monitor and control. Additionally, oil contamination can be assessed using oil mist detectors, which ensure that the air remains free from harmful hydrocarbons that could compromise product integrity. Particulate contamination can be evaluated through the use of particle counters, which help maintain the cleanliness of the compressed air system.
regular testing of compressed air quality is vital for maintaining system performance and preventing costly downtime. By employing a combination of moisture, oil, and particulate testing methods, organizations can ensure that their compressed air systems operate efficiently and effectively. It is important to establish a routine testing schedule and adhere to industry
Author Profile
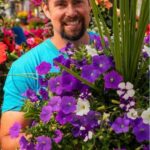
-
Michael Rigg is a visionary leader with a strong commitment to sustainability and environmental responsibility. With a wealth of experience in energy infrastructure decommissioning, land restoration, and corporate strategy. He has spent his career developing solutions that promote ecological balance while ensuring long-term industry viability.
Michael Rigg has always been passionate about sustainable agriculture, eco-friendly living, and renewable energy. He believes that sharing knowledge is the first step toward meaningful change. In 2025, he finally took the leap and began writing about these topics, offering informative posts and answering queries on issues that matter most to our readers.
Join us on this journey toward a greener future. Whether you’re just starting or already well versed in sustainability, there’s always something new to learn at Greenfield.
Latest entries
- April 13, 2025Farming QuestionsHow Many Yards of Soil Can Fit in a Dump Truck?
- April 13, 2025Recycling & WasteCan Wood Be Recycled? Exploring the Possibilities and Processes!
- April 13, 2025Recycling & WasteHow Can You Effectively Recycle Lightbulbs and Protect the Environment?
- April 13, 2025Eco-friendly livingAre Plastic Drinking Straws Recyclable? Unpacking the Truth Behind Their Environmental Impact